Building the Case For Block
CCMPA jumps into the conversation on resilient and sustainable building design.
#NetZero #PassiveHouse #Blockitout
Resilience has long been a buzz word in construction design and is used in a variety of ways; often without clear definition. For the purposes of this article, the definition will be derived from a paper by Norris, F.P., et al. titled “Community Resilience as a Metaphor, Theory, Set of Capacities and Strategy for Disaster Readiness”. Norris notes that “resilience is a process not just a result or outcome and resilience is adaptive (dynamic not static)”.
Further to this, the Federal Emergency Management Agency (FEMA) states that “resilience is the capacity of individuals, communities, businesses, institutions, and governments to adapt to changing conditions and to prepare for, withstand, and rapidly recover from disruptions to everyday life, such as hazard events”. Notably, this definition of true resilience echoes that of Norris above. In construction, ideally resilience starts with building codes, because they should aim to enhance public safety and property protection in the face of hazard events. Concrete masonry has long been recognized in building codes as essential to supporting this mandate of life safety. However, over the last several decades there has been a notable trend in building codes away from the mandated use of concrete masonry in favour of simply defined “non-combustible” alternate materials. This regression in building code rigour suggests a diluted focus on the true definition of resiliency, and lack of objective examination of all building materials, including concrete block.
It is common knowledge that increased building resilience is needed with the rapid onset of global warming, as well as increased frequency and intensity of natural disasters. In order to best address these climbing needs to resiliency, sustainable building design standards such as Net Zero or Passive House have continued to gain momentum in the design community. However, when we are designing to such rigorous standards, we need to ensure inclusion of building materials that are truly resilient, as defined by FEMA above. When designers and architects are selecting building materials, it seems that concrete block is often stereotyped as carbon intensive, archaic and unsightly – thereby excluded or overlooked in sustainable building design. However, as outlined below, many of the inherent properties in concrete block actually make it a leading building material of choice for truly sustainable and resilient design.
The speed of global warming is undeniably accelerating the demand for more sustainable buildings to help reduce our carbon footprint. But another piece of the building design puzzle is that global warming may be accelerating a spike in the frequency and severity of natural disasters. In order to best prepare for upcoming natural disasters or unforeseen events, we need to truly understand the world around us in its current state. Combining the definitions of Norris and FEMA above, exercising truly resilient building design means that we must demand designs and the use of materials that help communities prepare, withstand and rapidly recover. This preparation means gaining a true understanding of what our cities and communities can, and cannot, withstand in terms of natural disasters on social, economic and physical levels. Secondly, to be able to withstand the storm we need to engage in a continuous process of learning and improvement given the dynamic environment around us. Lastly, to assist with the rapid recovery of our communities and economy, we need to have clear plans in place which are sustainable and deliverable.
When discussing topics of climate change and natural disasters; it can also be argued that we need to broaden our lens on what are traditionally qualified as “natural disasters”: Fire, Flooding, Earthquakes and Hurricanes. As was stated by the US department of Health and Human Services, “Communities are increasingly complex, and so are the challenges they face. Human-caused and natural disasters are more frequent and costly. Factors like climate change, globalization, and increased urbanization can bring disaster related risks to greater numbers of people.” In the near future, added to this scope we may see global crisis such as the Covid-19 pandemic. The last two years have seen one unprecedented event after another, and living in a world that is changing this quickly means that we need to demand building standards that continually over perform and outlast even the unthinkable.
Layered on top of this immediate need for increased building resilience, is the precarious economic position in which Covid 19 has placed the world. With Canada’s recently released 2021 budget showing an unprecedented spend and deficit, it is clear that should a massive natural disaster occur without adequate preparedness the recovery cost could have astronomical impacts to the economy. For instance, in April 2016 the wildfire that devastated Fort McMurray is recorded by the Canada Disaster Database at an estimated recovery cost of $4,068,678,000, and was followed by flash flooding estimated at an additional $462,528,000. This translates to a total recovery cost of over $4.5 Billion dollars. With the Covid-19 pandemic layering economic instability on top of a global warming crisis our community resilience is being tested like never before.
The unique situation in which we find ourselves – a world facing accelerated climate change and the multitude of socio-economic challenges of a global pandemic – demands a holistic solution. When it comes to the built environment and the design for disaster resilience, the building design lens can no longer afford to overlook or under analyze any building material. As stated above, true resilience is an adaptive process, and the solution for the sustainability of our built environment is hybrid design which advocates multi-material design demanding each material be included where its strength outperforms the others. Below, this article will continue to outline the multitude of ways that concrete block not only supports sustainable and resilient building design as defined above, but in various cases can also perform beyond expectations.
What we know right now: (Why We Prepare)
To this point we have established three main points: first, the frequency, intensity and cost of natural disasters is increasing. Secondly, our communities are primarily built to the minimum building codes and standards. And third but definitely not least, the Covid-19 pandemic drove the global economy to an incredibly vulnerable position. Layering on top of all these challenges is the irrefutable fact that climate change is here now, and we need to make radical change to slow down the devastating impacts. The Biden administration is a clear example of one that takes climate change seriously. Immediately after his inauguration, President Biden re-started the Federal Interagency Council on Climate Preparedness and Resilience (EO 13653) which “will help identify how all federal agencies programs and operations can proactively address the current and predicted impacts of climate change, as well as how to avoid adding to vulnerabilities that already exist or will be exposed in the future”. The American Jobs Plan specifically states, “Every dollar spent on rebuilding our infrastructure during the Biden administration will be used to prevent, reduce, and withstand the impacts of the climate crisis.”
The US National Aeronautical Space Agency (NASA) released a report that investigates the evidence of climate change and states the fact that “the planet’s average surface temperature has risen about 2.12 degrees Fahrenheit (1.18 degrees Celsius) since the late 19th century, a change driven largely by increased carbon dioxide emissions into the atmosphere and other human activities. Most of the warming occurred in the past 40 years, with the seven most recent years being the warmest.” Evidence of the negative global impacts of this warming are irrefutable and can be seen in the rising frequency of natural disasters. For example, a common misconception in Canadian building design is that there is little to no seismic activity. However, the map below shows evidence to the contrary. With the rate of environmental change occurring at an exponential rate, design of our built environment must be stronger to keep us all as safe as possible.
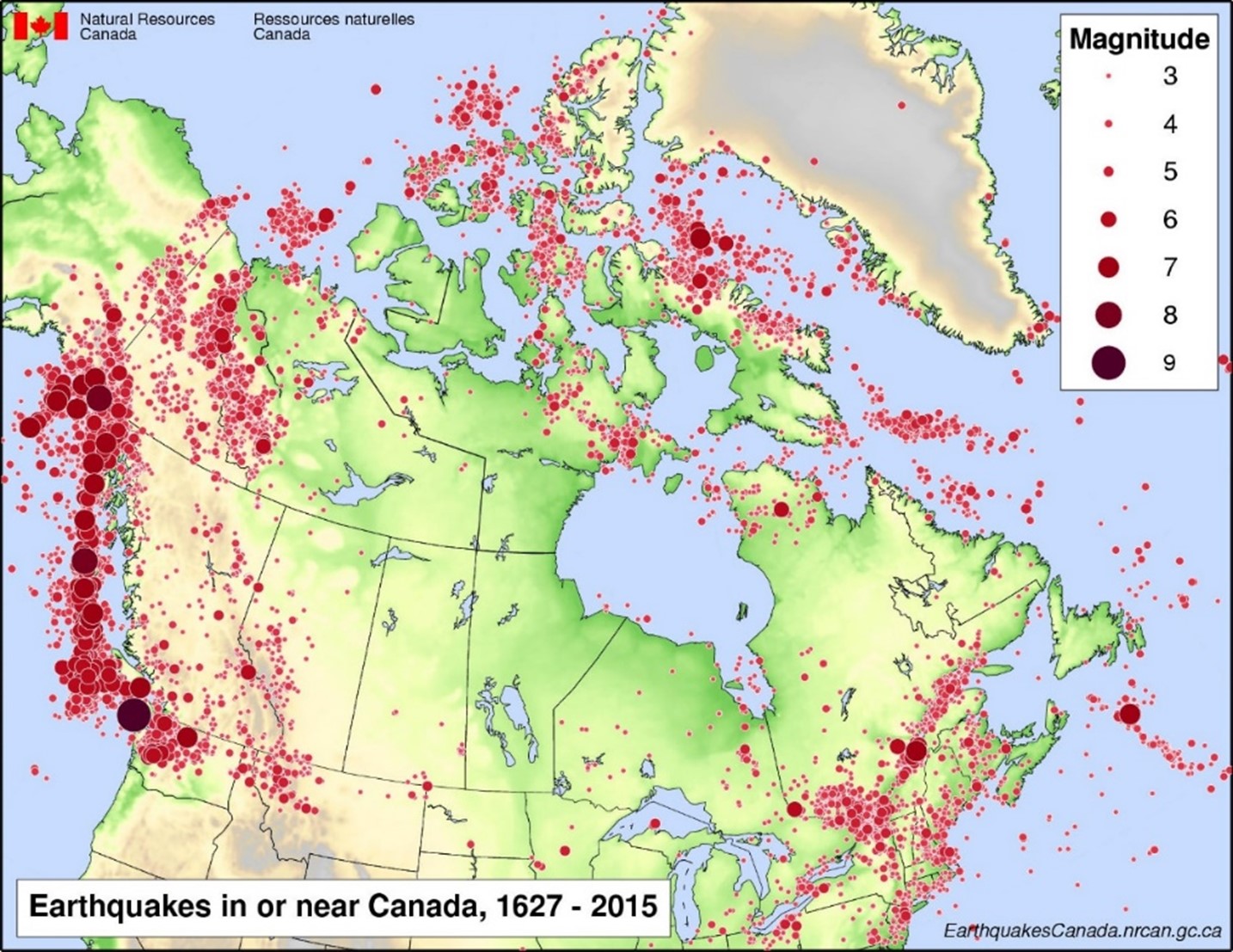
There are several industry experts in Concrete and Masonry who work actively to ensure that the National Building Code of Canada (NBCC) retains rigorous safety standards through each revision cycle (every 5 years). One of the continued primary areas of focus is fire resistance, and industry expert Steve Skalko maintains that “past fire history in the latter 1800s and early 1900s showed major fire conflagrations in populated metropolitan areas of Canada and the US wiping out whole sectors of cities when fire started in larger closely spaced wood frame buildings. Combined with wind, the fire moved quickly to destroy many buildings.” There is no shortage of examples where concrete block has saved the lives of both building occupants and emergency responders, such as firefighters, during a fire. One such example just occurred in Bradford, Ontario in April 2021. A six-storey hotel was being erected with primarily wood frame construction and concrete masonry stairwells and egress routes. An undetermined cause set the structure ablaze and after hours of firefighting, only the concrete masonry structure was left standing (see images below). Thankfully no one was harmed in the fire, but it clearly shows the difference in materials resistant to fire effects.
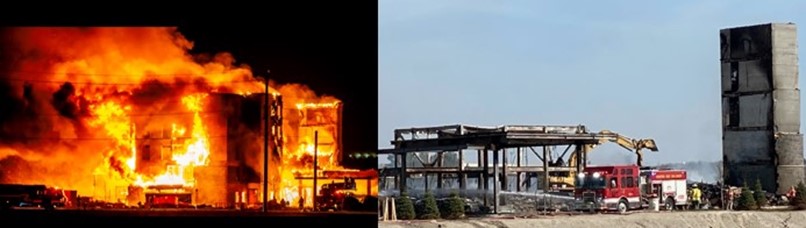
We need to continue to design and build structures that can preserve human life even under the greatest strain or the most intense occurrences. Only then will we have reached a building standard of true resilience as defined at the outset of this paper. However, Gary Sturgeon counters that “building resilience is much more than simply preserving human life (or life safety). The codes presently focus on life safety. Where they fail currently is by not suitably addressing resilience”.
Overall, it seems that the multitude of demands and varying criteria facing anyone in the design space; designers, architects, structural engineers and urban planners, makes truly sustainable and resilient design extremely difficult. There are just too many needs to be met when designing our built environment. To design and build with resiliency today, and for our future, one must figure out how to build above-code to withstand increasing natural disasters, ensure economic viability, making choices that support sustainability and drive the continued reduction of greenhouse gas emissions throughout the entire process; all the while making sure the design is aesthetically pleasing. It’s an impossible ask. Or is it?
What we are learning: (How we will withstand)
To start, we know that there is a long list of merits to building with concrete block. Particularly when the conversation turns to natural disasters, concrete block is at the forefront of selected building materials. According to an article by the Concrete Network; “Concrete Safe Rooms & Storm Shelters” when the average storm hits you have less then 13 minutes to seek shelter. Further to this, “For people living in wood-frame homes without basements, that “safe” place often ends up being an interior room, such as a closet or bathroom, with no windows. But in a powerful tornado or hurricane packing winds of more than 250 miles per hour, even well-constructed frame houses can be lifted right off their foundations, and large debris can turn into airborne missiles. During such extreme conditions, one of the safest places you can be is in a storm shelter, or safe room, constructed of reinforced concrete or concrete block with no windows and a concrete floor or roof system overhead”. Given the inherent strength in concrete masonry wall systems, block seems an obvious choice for storm shelters, safe rooms, elevator shafts and egress routes.
Despite the well documented physical attributes of concrete block, as climate change evolves and progresses, we are forced to look for solutions with fresh, or at least reimagined, perspectives in order to find creative solutions. In following with this thought, it can be argued that fundamental change, or reimagination, of how we utilize concrete block in building design, specifically regarding codes and specifications, could also play a critical role in helping slow the rate of global warming.
Thanks to the relentless efforts of countless environmental organizations and activists, it does seem like finally the world is listening and acting in response to the aggressive onset of global warming. On March 25th, 2021, in a 6-3 vote, the Supreme Court of Canada voted to pass the Carbon Emission tax. The fee could climb as high at $170/tne by 2030. This decision was driven forward when “Parliament passed the Greenhouse Gas Pollution Pricing Act in 2018, based on the consensus that greenhouse gas emissions contribute to global climate change. Countries around the world committed to drastically reduce their greenhouse gas emissions under the 2015 Paris Agreement. In Canada, the federal government passed the Act to implement its commitments”.
Typically, where there is a conversation about carbon emissions, the topics of concrete and cement are never far behind. Concrete is the 2nd most utilized material in the world (second only to water), and cement alone contributes an estimated 7% of all global emissions. Understanding the magnitude of their carbon footprint, the cement and concrete industries are responding by reducing and reinventing. For example, the Global Cement and Concrete Association has designed an aggressive strategic plan which is driving towards carbon neutral production by 2050. In Canada, concrete block producers are working very hard to support these initiatives with various plant retrofits, raw material and production process changes. In 2020 research revealed that over 70% of concrete block in Canada was produced with lower carbon cements (such as Portland Limestone Cement / GUL). This change alone resulted in a 10% reduction in the carbon footprint in CMU production. Producers are not only adjusting the materials in their processes, but also reassessing the processes themselves.
Where we are going: (How we will recover & sustain)
So far this article has established the multitude and complexity of challenges that face the design of our built environment today. As seen above, the three largest challenges today are increased severity and frequency of natural disaster events, carbon emissions and sustainability. Outlined below are a few key points to elaborate on these challenges and clearly demonstrate that to out design these challenges we need to view all elements of design through a fresh perspective, and a reexamination of concrete block as a key building material in achieving the complexity of demands for the built environment of tomorrow.

I would suggest if a fresh design perspective were applied to concrete block, that instead of seeing an archaic, carbon intensive and aesthetically unpleasing building material, that we might instead see the leading building material in US Disaster resilient design builds, the lowest carbon causing concrete product in Canada, and a product with physical properties that inherently support forward thinking design such as Passive House or Net Zero buildings.
First – Over the last decade the loss of life from natural disasters has dropped notably in North America, but the cost of recovery has skyrocketed. National Institute of Building Sciences (NIBS) explains that building codes set minimum requirements to protect life safety when met. However, in addition to the cost of human life, is the financial impact of disaster recovery, and NIBS estimates that above-code design could save $4 per $1 cost at the outset of construction. Understanding that we are living in a world where the spectrum of natural disasters seems to only continue to increase in severity, mitigating this cost both in terms of human life and financial repercussions, should be included into the design conversation.
Second – Carbon emissions are clearly a large challenge for the concrete and cement industries. This will require an aggressive and relentless pursuit at reduction if for no other reason than to reduce the impact of the recently pass Emission tax in Canada (March 2021). In addition to the example of utilizing lower carbon options in concrete that was outlined above, there are also several carbon sequestering properties that are being discovered in concrete. In an article by Peter Coy in Bloomsberg Business Week, entitled “Locking Carbon Dioxide into Concrete is a Cool idea”, he argues that “One of the coolest green ideas is to offset some of cement’s massive carbon dioxide emissions by putting carbon dioxide to good use in the production of concrete. It usually takes concrete a few weeks to reach maximum hardness, but injecting carbon dioxide speeds up the so-called curing process. The carbon dioxide becomes mineralized—and thus immobilized–by reacting with calcium ions in the cement.” This is just one example of the ways that the concrete block industry is showing they can pivot and adapt to changing conditions, all the while continuing to provide the inherent resilience and durability that has always defined it as a leading building material.
Third – Building design is clearly moving in a direction which supports a more sustainable, energy efficient, environmentally friendly and holistic approach than ever before. Concepts such as Passive Haus (Passive House) Standard sets out the criteria for quality, comfortable and energy efficient homes. The Standard is overseen by the Passive House Institute, which was established in Germany during the 1990s by Wolfgang Feist. Arguably, the physical properties and installation of concrete block inherently supports the rigorous demands of this design standard, particularly in terms of thermal mass, airtightness and acoustics.
Perhaps a more common building standard, Net Zero Homes, has been proven to be 80 percent more energy efficient than typical new homes and use renewable energy systems such as solar panels, to produce the remaining energy they need. And again, concrete block has several inherent physical properties which wholly support the demands of this design.
GREAT! BUT CONCRETE BLOCK IS UGLY.
In an article by Eric Baldwin, “Laid Bare: 5 Stunning Projects Using Concrete Blocks”, he tackles several of the challenges outlined above, notably including the aesthetics of block. Eric states “Concrete blocks often get a bad rap. The raw, industrial appearance of a concrete masonry unit (CMU) is often characterized as having a “plain” or basic aesthetic, and it must be correctly detailed to avoid sustained water damage or foundation buckling. But, when designed and assembled properly, concrete block constructions are stronger than poured concrete, and can transform the performance of a building envelope.” Given the scope and complexity of the challenges facing architects and designers in the current world, perhaps the answer is actually quite simple: go back to basics.
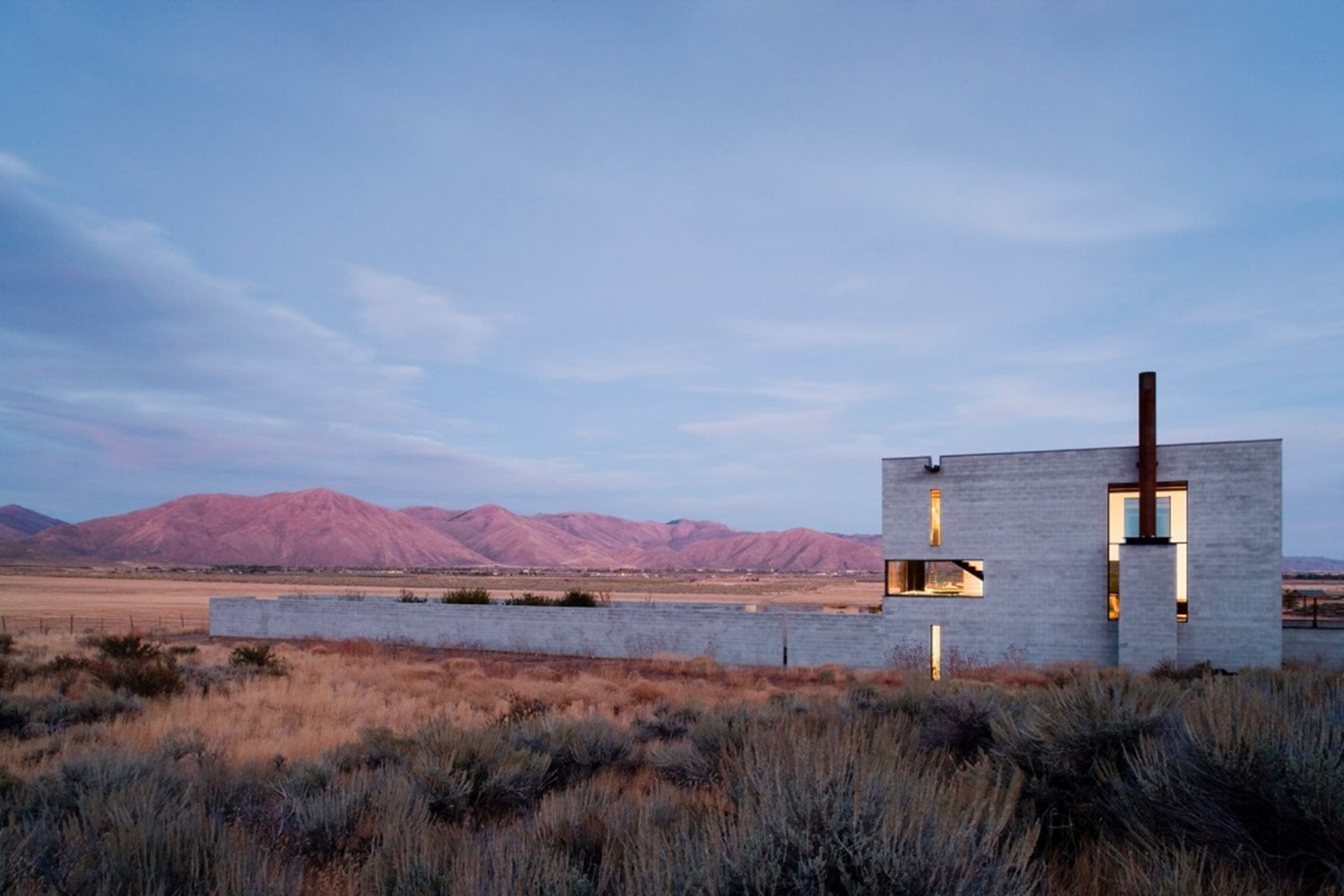
One of the projects highlighted is Outpost, by Olson Kundig Architects in the Idaho high desert; “Outpost utilizes thick concrete walls made from concrete block, as well as materials like car-decking and plywood. The concrete masonry blocks were combined to create the footprint of the house and limit intrusion into the land. The readily available construction material allowed commercial builders to quickly and cheaply assemble the building, creating an experience of place”. The concrete blocks are used with a range of shapes and sizes to create fire-resistant, durable and virtually soundproof walls. They also help mitigate energy usage and play with light and shadow to transform exterior façades. As versatile units, the blocks can double as structural frames and base systems for veneer applications.
In conclusion, while the inherent merits of concrete block are clear from the facts above, as an industry we can still only conceptively make this argument. There seems to be a significant lack of data or research that can definitely support the use of concrete masonry and concrete block as primary building materials to support the specific building design standards focused on sustainability, notably Net Zero Buildings and Passive House design. The Canadian Concrete Masonry Producers Association (CCMPA), as representative of concrete block producers across the country, has a strong commitment to reducing our carbon footprint in both processes and finished products. Further to this, we believe that concrete block is a natural building material of choice when discussing design demands around thermal mass, acoustics and carbon sequestering. To this end, in an attempt to fill the data gap, we have partnered with Masonry Works, in collaboration with NCMA and 3DIQ, designing a research internship focused solely on objectively investigating the merit of concrete masonry and block in sustainable design. We recruited the successful candidate from the University of Waterloo Masters of Architecture program. Our internship will run 17 weeks and we are looking forward to seeing what our student unearths about how concrete masonry can help support commercial, residential and mixed use building sustainable design.
And this is not all we are doing!
CCMPA is committed to supporting the block market and our members, so we have commissioned 2021 studies to investigate the Insurance Cost Trends in Concrete Versus Wood Buildings (Frank T. Came & Associates), A Comparative Life Cycle Analysis (LCA) of Building Materials (University of Windsor), and a comparative look at the Initial Cost of Construction in Multi-Residential Structures (Walter G. M. Schneider III).
Our 2021 goal is that the combination of these studies comprised of current day data, work together to make the irrefutable case for concrete block as a resilient, cost-effective and sustainable building material that should be integrated into all sectors of building design.
These studies will be released as completely and presented at our quarterly Board & Member meetings. On June 10th, 2021 we welcome Walter G. M. Schneider III to present his findings for Toronto, Ontario in the Initial Cost of Construction in Multi-Residential Structures.
As always, if you have any comments, questions or recommendations, you can reach us at Info@CCMPA.ca
- https://www.phe.gov/Preparedness/planning/abc/Pages/community-resilience.aspx
- https://www.theglobeandmail.com/opinion/article-to-avoid-a-climate-disaster-governments-must-do-these-seven-things-and/
- https://gccassociation.org/wp-content/uploads/2020/09/GCCA_ClimateAmbitionStatement_Print_AW.pdf
- https://www.worldwildlife.org/projects/biogenic-carbon-footprint-calculator-for-harvested-wood-products
- https://www.fema.gov/sites/default/files/2020-03/fema-strategic-plan_2018-2022.pdf
- https://cdn.ymaws.com/www.nibs.org/resource/resmgr/reports/mitigation_saves_2019/ms_v4_overview.pdf
- https://www.getprepared.gc.ca/index-eng.aspx?utm_campaign=ps-sp-emergencypreparedness-20-21&utm_medium=sem&utm_source=ggl&utm_content=ad-text-en&utm_term=natural%20disasters%20in%20canada&adv=2021-0093&id_campaign=12477171746&id_source=118938646939&id_content=503170348787&gclid=Cj0KCQjwjPaCBhDkARIsAISZN7TAxe-8C_hJyA_ZuhrYAgek6GXhDGKFS3beJvrhwPhzsAVe0pgyrbEaAm2jEALw_wcB&gclsrc=aw.ds
- https://earthquakescanada.nrcan.gc.ca/historic-historique/caneqmap-en.php
- https://www.fema.gov/sites/default/files/documents/fema_planning-resilient-communities_fact-sheet.pdf
- https://cdd.publicsafety.gc.ca/rslts-eng.aspx?cultureCode=en-Ca&boundingBox=&provinces
- https://climate.nasa.gov/evidence/
- https://www.scc-csc.ca/case-dossier/cb/2021/38663-38781-39116-eng.aspx
- https://www.cbc.ca/news/politics/supreme-court-federal-carbon-tax-constitutional-case-1.5962687
- https://www.bloomberg.com/news/articles/2020-12-14/locking-carbon-dioxide-into-concrete-is-a-cool-idea#:~:text=One%20of%20the%20coolest%20green,the%20so%2Dcalled%20curing%20process.
- https://www.constructioncanada.net/wood-in-civic-buildings/?qnewsletter=20210127&en_click=1&utm_campaign=2021-01-27&utm_medium=email&utm_source=newsletter&utm_content=features
- https://architizer.com/blog/inspiration/collections/cmu/
- https://ncma.org/resource/concrete-masonry-hurricane-and-tornado-shelters/
- https://ccmpa.ca/2014/03/a-concrete-firewall-protected-the-residence-du-havre-seniors-home-in-lisle-verte/
- https://www.nrdc.org/experts/rob-moore/promise-climate-resilience-and-president-bidens-jobs?utm_content=162154536&utm_medium=social&utm_source=linkedin&hss_channel=lis-tat6LTPIOt
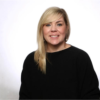
Written by: